The bgm Smallframe Gear wheels, main and auxiliary shafts are manufactured in Europe under high quality requirements. In addition to the high-quality material used, the remuneration of the components also plays a major role. Therefore, all transmission parts such as gear wheels, auxiliary shaft, main shaft as well as the shift dog are individually remunerated at Thyssenkrupp. The high-quality material, the dimensional accuracy due to the precise production and the "know how" in the treatment create an extremely resilient gear part.
stress test
In order to ensure that the gear wheels can withstand high loads over the long term, the components were subjected to a load test in a German test laboratory for gear drives.
To explain this roughly with an example:
The bgm Gear III was subjected to a pulsating load of 64.000kN with 8 load changes until the provoked failure. With a lower test load, i.e. less than 8kN, no failure could be generated during the test. For comparison; a third gear from a Piaggio transmission failed in this test after 33.000 load changes. This means that the fatigue strength of third gear is at bgm about 90% higher than the original Piaggio component.
If you translate this laboratory test as driving performance on the road, this test load corresponds to an engine with over 50Nm torque on the crankshaft, which is driven at full throttle for a little more than 1000km at a time.
The bgm Smallframe Gear wheels are available in the familiar gradation of 58, 54, 50, 46 and 48 teeth. The tooth profiles of bgm Gears are based on the Piaggio gear wheels of the gear type with the marking "42" and thus have the bgm Gears also have the same range of use as the Piaggio original gearbox. An exception is the fourth gear with 48 teeth. This gear may only be combined with countershafts with 22 teeth on the fourth gear.
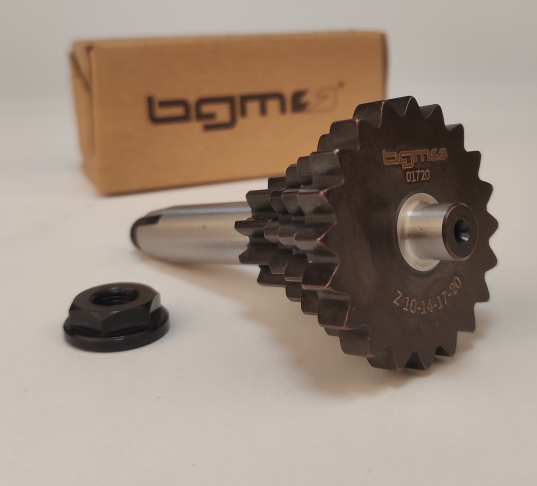
We offer matching auxiliary shafts with three different gradations for the gear wheels:
bgm01822: 10-14-18-22
the original gradation,
Everyone can be on this secondary wave bgm, as well as gear wheels that correspond to the type 42 gearbox. So also gear wheels, for example from Benelli, Fabbri, OEM which are suitable for the original Piaggio gearbox.
bgm01821; 10-14-18-21
The “Short Fourth Course”
Here the jump between third and fourth gear on fourth gear is one tooth shorter. The speed difference when shifting from third gear to fourth gear is reduced by approx. 400 rpm and helps to achieve a better gear connection. If the same top speed is to be achieved in fourth gear at the same engine speed, a primary 27/69 (2:56) with a primary wheel z28 can be used. The top speed remains the same, but with the advantage of a better connection when shifting from gear three to gear four. This countershaft can only be used with the fourth gear with 46 teeth on the mainshaft. By reducing one tooth in fourth gear, this countershaft is the most sensible way to shorten the gear jump. By distributing only 21 teeth on the same diameter of the auxiliary shaft, the tooth bases are significantly wider and therefore more stable. The combination with this auxiliary shaft in fourth gear (46:21 = 2.19) roughly corresponds to the use of the short fourth gear with 48 teeth on the main shaft with an original auxiliary shaft
(48:22 = 2.18), but is much more durable.
bgm01720: 10-14-18-20
The gradation short third gear, short fourth gear
The jump from gear two to gear three and from gear three to gear four is significantly reduced. Can also only be used for type 42 gear wheels. Compared to the original gradation, the third gear is one tooth shorter and the fourth gear two teeth shorter. As with the auxiliary shaft with the short fourth gear, this makes the teeth on the third and fourth gear more stable due to wider tooth bases. "THE" auxiliary shaft for fast and high-torque engines, which are equipped with a long primary reduction or are clearly speed-oriented with a short primary reduction.
The bgm Pro side shafts
The bgm Pro side shafts are just like that bgm Pro gear wheels manufactured and tested under high requirements. For example, in direct comparison to a Piaggio auxiliary shaft, the third gear is the bgm Per auxiliary shaft in the durability test with 150.000 load changes and the Piaggio auxiliary shaft with 58.000 load changes in the pulsator test.
In comparison, the third gear is the bgm Countershaft more than 150% longer than an original Piaggio countershaft. A significant increase in safety for engines with an increase in performance.
In the future, the gearboxes will also be fully assembled with shoulder rings, reinforced shift springs, our new one bgm Pro Sport shift dog available. The game of the gear wheels is through the matching ones bgm Pro shoulder rings precisely adjusted and the main shaft can be mounted directly.
Transmission (gear wheels incl. main shaft)
With the bgm Pro gearbox for the Vespa Smallframe, we provide you with an extremely resilient solution for your gearbox. This is possible thanks to the available variants bgm Individually tune each transmission to almost all engine concepts and personal preferences in the ride shops.
bgm shift claw
bgm PRO SPORT - 4 speed, H=50mm,
VESPA PK50, PK80, PK125, V50 (V5A1T from 69444), Special (V5B3T from 94315), Elestart (V5B4T from 1514), PV125 (VMA2T from 150203), ET3 (VMB1T from 8161)
BGM PRO has given the successful BGM6550 shifter an update. The successor BGM6555 has a completely redesigned locking profile. This means that the gears are even more precise and the dreaded gear jumping is completely prevented.
The BGM Pro shift claw is made of high quality 15CrMo5 (SCM415) chrome molybdenum steel and is therefore very durable. The flanks have very narrow tolerances compared to the shifting claws otherwise available on the market. This guides the claw precisely in the main shaft and effectively prevents it from twisting/tipping.